Titanium CNC Machining: Key Techniques for Achieving Precision and Durability
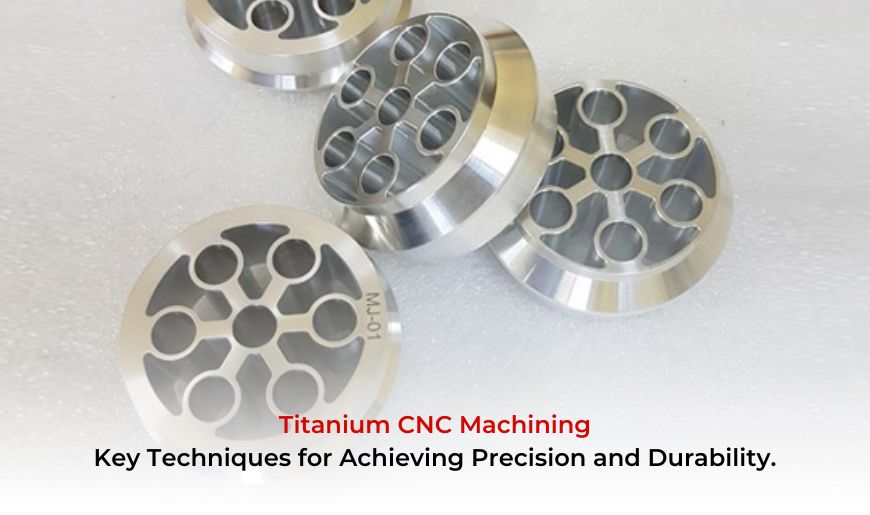
When it comes to tough, lightweight, and high-performance materials, titanium is a top contender in many industries. But machining titanium isn’t as simple as cutting through softer metals. This material poses unique challenges, from its strength and toughness to its tendency to heat up quickly during the machining process. Yet, the demand for titanium in industries like aerospace and medical devices continues to rise, making mastering titanium CNC machining a critical skill for manufacturers.
Manufacturers often choose titanium for its impressive strength-to-weight ratio, corrosion resistance, and ability to withstand extreme temperatures. These qualities make it indispensable in applications where reliability and durability are paramount. But machining it to tight tolerances requires a deeper understanding of the techniques and technologies involved. So, what makes titanium machining a bit more challenging—and how do manufacturers get it right?
The key to machining titanium lies in precision, tool selection, and controlling the heat generated during the process. Because titanium is not only strong but also somewhat “sticky” to cutting tools, it’s easy for the material to create excessive friction, causing tools to wear out faster and the material to overheat. This can lead to surface imperfections, reduced tool life, and a lower quality final product. Let’s explore the key techniques used to achieve precision and durability when machining titanium.
Tooling Choices Make All the Difference
One of the most important factors in titanium machining is selecting the right cutting tools. Manufacturers often avoid standard carbide tools for titanium; instead, they use specialized tools with coatings like TiAlN (titanium aluminium nitride) or CVD (chemical vapor deposition). These coatings help reduce friction and improve the tool’s ability to withstand the high temperatures generated during the machining process.
Beyond coating, the geometry of the tool matters too. Cutting tools with sharper edges and proper angles are more effective at minimizing heat generation and ensuring smooth cuts. This is crucial because titanium’s strength makes it harder to machine, and improper tool selection can lead to issues such as excessive wear, tool breakage, or poor surface finish.
Speed and Feed Rates: The Balancing Act
In titanium machining, there’s a delicate balance between cutting speed and feed rate. Titanium requires lower cutting speeds compared to other metals, such as aluminium, because it tends to absorb heat quickly. Going too fast can cause the material to overheat, leading to poor surface finishes and even tool failure. On the other hand, manufacturers must adjust feed rates to ensure that the cutting tool engages with the material properly without causing unnecessary strain.
Getting this balance right is an art. CNC machines specializing in titanium often use advanced controls to help operators fine-tune speed and feed rates based on the specific titanium alloy. Lower speeds with high feed rates allow for greater control over material removal, which results in a more consistent and precise final product.
Managing Heat: Cooling Is Key
Titanium is notorious for generating heat during machining, which can quickly damage both the material and the tool. As titanium is cut, the heat is concentrated at the cutting edge, making it essential to have an effective cooling system in place. Using a combination of coolant and mist is common practice to keep temperatures under control and ensure that both the titanium and the cutting tools remain within optimal temperature ranges.
The use of high-pressure coolant systems is especially useful, as they direct coolant precisely to the cutting edge, preventing heat build-up and improving tool life. This also helps reduce the formation of burrs and other imperfections on the titanium’s surface. For manufacturers, this means better surface finishes, longer tool life, and greater overall precision.
Toolpath Strategies for Optimal Results
One of the main aspect of machining titanium is the toolpath strategy. Titanium requires careful planning in terms of how the cutting tool moves through the material. Since titanium is a tough material, using aggressive cutting strategies or deep cuts all at once can lead to excessive tool wear or even part distortion.
Instead, manufacturers often employ strategies such as light, multiple passes with shallower cuts to minimize stress on the material and the cutting tool. Additionally, using constant engagement cutting techniques—where the tool maintains contact with the material for a consistent period—can help avoid sudden temperature fluctuations, keeping both the material and the machine running smoothly.
Finishing Touches: Surface Quality Matters
Achieving a high-quality finish on titanium parts is a meticulous task. As titanium is prone to surface imperfections if not machined correctly, finishing processes like grinding or polishing are often necessary. A smooth surface finish isn’t just for aesthetics—it’s crucial in many industries, especially in aerospace and medical device applications, where even the slightest flaw could cause performance issues.
To achieve a fine surface finish, careful attention is paid during the final stages of machining. This involves fine-tuning feed rates, speeds, and cutting depths, ensuring that the tool engages with the material in the most efficient way possible. Post-machining treatments, such as polishing, are often employed to ensure that the surface meets the strictest specifications.
Why Titanium CNC Machining Matters
In industries like aerospace and medical titanium parts are put through rigorous stress tests. Whether it’s a critical part of an airplane engine, a prosthetic implant, or a lightweight automotive component, precision titanium machining ensures the durability, strength, and reliability of these parts. By mastering the right techniques—whether it’s the proper tooling, heat management, or finishing methods—manufacturers can produce high-quality titanium components that meet the exacting demands of these industries.
Ultimately, titanium CNC machining requires a fine balance of skill, knowledge, and technology. The right techniques ensure that titanium components are not only precise but also durable enough to stand the test of time, regardless of how harsh the conditions might get. So the next time you encounter a titanium part—whether it’s an aircraft component or a medical device—remember that its performance is a direct result of these carefully honed machining techniques. Unlock the Power of Titanium Machining! Maximize efficiency and quality with advanced techniques. Get in touch now!