Top Mistakes to Avoid When Designing Machined Components
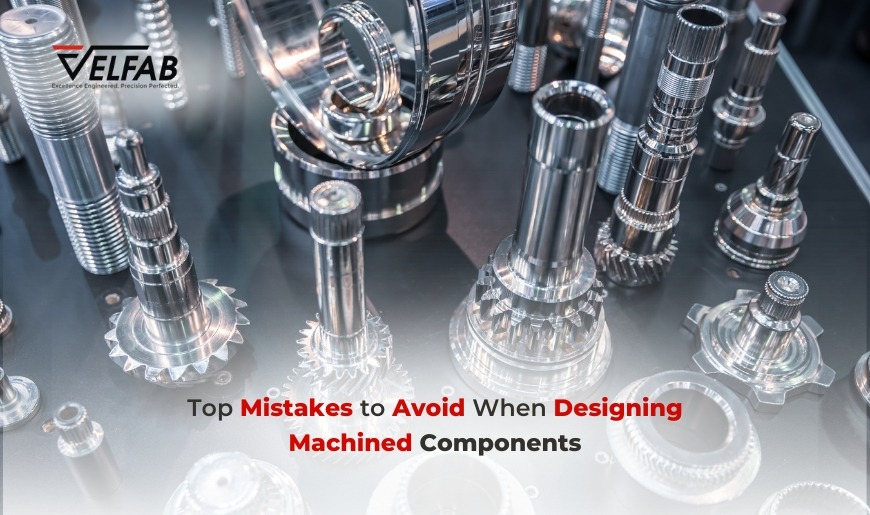
Designing machined components is a balancing act between functionality, cost, and manufacturability. Even small design oversights can lead to higher production costs, extended lead times, or even manufacturing failures. At Velfab, we emphasize the importance of DFM (Design for Manufacturability) in machining to help our clients create parts that are efficient, cost-effective, and easy to produce.
If you’re designing components for CNC machining, here are some of the most common mistakes to watch out for—along with practical design tips for turning and milling.
1. Overly Tight Tolerances in Machined Components
Yes, precision matters. But specifying unnecessary tight tolerances for non-critical features can significantly increase machining time and costs. Tighter tolerances often require additional inspection, specialized tooling, and more precise setups, all of which add to production expenses.
What to do instead:
Only apply tight tolerances where absolutely necessary. For other areas, use standard tolerances that still meet performance requirements without driving up costs.
2. Choosing the Wrong Material
Not all materials machine the same way. Some metals and plastics are easy to cut, while others wear down tools quickly or require specialized machining techniques. Picking a material without considering its machinability can lead to slower production times, higher tool wear, and increased costs.
What to do instead:
Consult with your machinist early to choose a material that balances performance, durability, and cost-efficiency.
3. Designing Thin Walls
Thin walls can lead to structural weaknesses and make machining difficult due to vibrations and deflection. If a wall is too thin, it can flex during cutting, resulting in inaccuracies or even breakage.
What to do instead:
Stick to recommended wall thicknesses for the chosen material. If lightweighting is necessary, use ribs or supports to maintain strength.
4. Ignoring Tool Accessibility
If a cutting tool can’t reach a certain area of your design, you’ll need additional setups, special tooling, or even redesigns—all of which add cost and complexity. Deep pockets, narrow slots, and sharp internal corners can create accessibility issues in machining.
What to do instead:
Ensure all features are reachable by standard cutting tools. If deep pockets are required, consider adding fillets to internal corners and minimizing unnecessary depth.
5. Using Non-Standard Hole Sizes
It might seem like a small detail, but using non-standard hole sizes can force machinists to use custom tooling, which increases costs and production time.
What to do instead:
Whenever possible, aim to design holes that align with standard drill sizes. This helps avoid the hassle of custom reaming or boring, making the process smoother and more efficient.
6. Specifying Unnecessary Surface Finishes
A mirror-like finish might look great, but achieving ultra-smooth surfaces often requires additional machining steps, which can drive up costs. Some finishes also impact part functionality, especially in high-friction environments.
What to do instead:
Determine the necessary finish for your part based on its application. Avoid excessive polishing or finishing unless it’s functionally required.
7. Not Consulting Your Machinist Early
One of the biggest mistakes is waiting until the design is finalized before getting input from a machinist. Simple adjustments early in the design process can have a huge impact on cost savings and ease of manufacturing.
What to do instead:
Work with your machining partner from the start. A quick DFM review can save you time, money, and frustration down the road.
Final Thoughts
Avoiding these common mistakes can lead to better, more cost-effective machined components. Whether you’re designing parts for prototyping or full-scale production, following these design tips for turning and milling will ensure a smoother CNC machining process.
At Velfab, we specialize in precision CNC machining and help clients optimize their designs for manufacturability. If you’re working on a new project, reach out to us—we’re happy to offer insights to make your design more efficient and production-friendly!