Choosing the Right Materials for Precision CNC Machined Parts
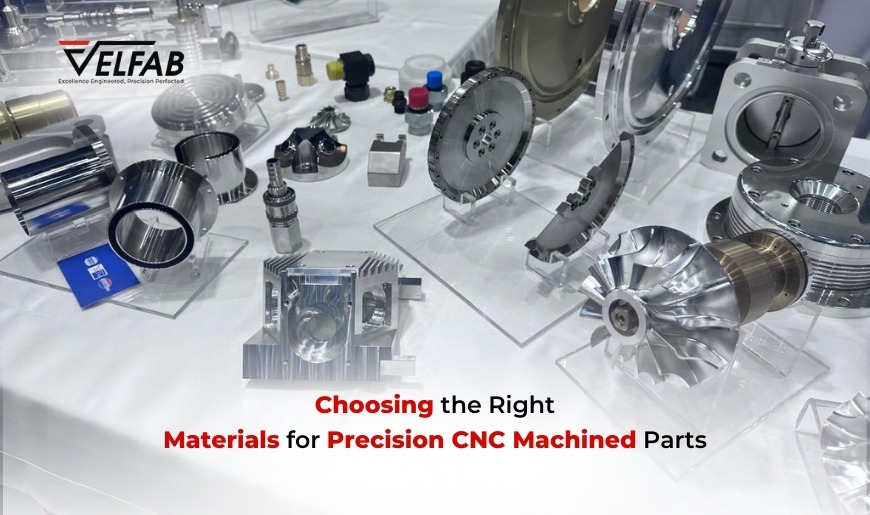
Choosing the appropriate materials for precision CNC machined parts is crucial to ensure optimal performance, durability, and cost-effectiveness. The material selection impacts not only the functionality of the component but also the efficiency of the machining process itself. In this guide, we will explore key considerations to help you make informed decisions when selecting materials for precision CNC machined parts.
Understanding Material Properties
The first step in material selection is understanding the specific properties required for your application. Consider the following factors:
- Mechanical Properties: Assess the strength, hardness, and toughness needed. For instance, components subjected to high stress may require materials like alloy steel or titanium.
- Thermal Properties: Determine the operating temperature range. Materials like stainless steel or certain ceramics can withstand high temperatures without degrading.
- Corrosion Resistance: For environments prone to moisture or chemicals, materials such as stainless steel or specific polymers offer superior corrosion resistance.
- Weight Considerations: In applications where weight is critical, lightweight materials like aluminum or magnesium alloys are preferable.
Machinability of Materials
The ease with which a material can be machined—its machinability—significantly affects production efficiency and cost. Materials with high machinability require less power to cut, produce a better surface finish, and extend tool life. Here’s how common materials rank:
- Aluminum Alloys: Known for excellent machinability, making them ideal for high-speed machining operations.
- Brass and Copper: These materials also offer good machinability and are often used in electrical components.
- Carbon and Alloy Steels: Machinability varies; low-carbon steels are easier to machine than high-carbon or alloy steels.
- Stainless Steels: Generally more challenging to machine due to their hardness and tendency to work-harden.
- Titanium and Nickel Alloys: These are difficult to machine and require specialized tooling and processes.
Choosing materials with higher machinability can reduce production time and costs. However, this must be balanced against the material’s performance characteristics required for the application.
Material Availability and Cost
The availability and cost of materials are practical considerations that can influence material selection:
- Standard Sizes and Forms: Materials available in standard sizes (e.g., bar stock, plates) can reduce waste and machining time.
- Cost Factors: While materials like titanium offer excellent properties, they are more expensive than alternatives like aluminum or steel.
- Supply Chain Reliability: Ensure the chosen material is readily available to prevent delays in production.
Surface Finish and Tolerances
The required surface finish and dimensional tolerances can influence material choice:
- Surface Finish: Some materials achieve desired finishes more easily. For example, aluminum can attain a high-quality finish with minimal effort.
- Tolerances: Materials that are stable during machining, like certain steels, are better suited for components requiring tight tolerances.
Environmental and Regulatory Considerations
Consider environmental factors and compliance with regulations:
- RoHS Compliance: Ensure materials meet the Restriction of Hazardous Substances standards, especially for electronic components.
- Recyclability: Materials like aluminum are highly recyclable, aligning with sustainability goals.
Conclusion
Selecting the right material for precision CNC machined parts is a multifaceted decision that impacts the performance, manufacturability, and cost of the final product. By thoroughly assessing the mechanical properties, machinability, availability, cost, and environmental considerations, you can make informed choices that align with your project’s requirements. Collaborating with experienced manufacturers, such as Velfab Engineers, can provide valuable insights and ensure that your material selection leads to successful and efficient production outcomes.