How Aluminium Castings Drive Efficiency in Large-Scale Manufacturing
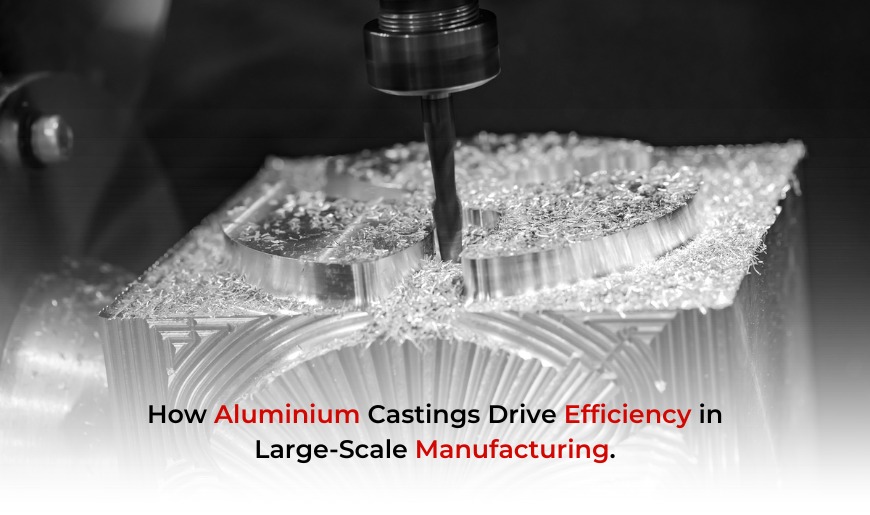
In the world of large-scale manufacturing, time is money. Every minute saved, every step streamlined, and every cost reduced adds up to big wins. So, it’s no surprise that manufacturers are constantly on the lookout for smarter ways to get the job done faster, cheaper, and better. One of the unsung heroes of this push for efficiency is aluminium casting.
Aluminium castings are revolutionizing industries by making production processes smoother, cost-effective, and environmentally friendly. But how exactly does something as simple as aluminium make such a difference in today’s high-demand manufacturing environments?
Let’s dive into the ways aluminium castings are driving efficiency in large-scale production.
Aluminium in Manufacturing
Aluminium is one of those materials that seem to do it all. It’s lightweight, strong, and resistant to corrosion, which makes it ideal for casting. The real power of aluminium lies in its ability to be molded into complex shapes without sacrificing strength or quality. Whether it’s intricate automotive parts or aerospace components, aluminium castings offer manufacturers a unique blend of precision and practicality.
The casting process, where molten aluminium is poured into molds, allows for the creation of parts that are both lightweight and durable. This means manufacturers can produce large volumes of parts without the hefty costs typically associated with other materials. When every penny counts in manufacturing, aluminium’s versatility and efficiency make it a top choice.
Speeding Up Production with Less Effort
One of the most significant advantages of aluminium casting in large-scale manufacturing is how it speeds up production. In many industries, time is a critical factor, and aluminium casting helps shave off those precious minutes. The process is highly efficient, allowing manufacturers to create complex parts in a single step with minimal need for additional machining or post-production work.
For instance, in the automotive industry, where companies produce thousands of vehicles annually, using aluminium castings helps minimize assembly time. This not only saves on labor costs but also helps manufacturers get products to market faster.
Lightweight Strength with Less Material
One of the reasons aluminium casting has become so popular is because it produces strong but lightweight parts. This is a game-changer, especially in industries where weight plays a crucial role.
The best part? aluminium is easy to mold into complex shapes. This means manufacturers can produce intricate parts like cooling channels for engines or delicate frames for machinery in a way that would be more challenging (and costly) with other materials. The flexibility of aluminium casting allows for innovation without sacrificing cost or quality.
Going Green
Aluminium castings also have a sustainable side that’s impossible to ignore. As the world pushes toward more eco-friendly practices, aluminium’s recyclability gives it a major advantage. Aluminium can be recycled again and again without losing any of its qualities, and that’s something manufacturers are increasingly tapping into.
Instead of throwing away scrap aluminium, many manufacturers recycle it back into the casting process, reducing the need for new raw materials. Not only does this lower material costs, but it also reduces the environmental impact of production. In fact, producing aluminium from recycled scrap uses only a fraction of the energy required to create new aluminium from ore, making it a far greener option for large-scale manufacturing.
Durability and Long-Term Reliability
Another compelling reason for using aluminium castings is their durability. aluminium parts resist corrosion better than many other metals, making them perfect for applications where parts are exposed to harsh conditions. Whether it’s engines that have to withstand extreme heat or outdoor machinery exposed to rain and snow, aluminium castings hold up over time, reducing the need for frequent repairs or replacements.
Looking Ahead
As manufacturers continue to push for greater efficiency and sustainability, aluminium castings will remain a vital part of the puzzle, helping companies meet the demands of the future while maintaining a competitive edge. Aluminium castings are far more than just a cost-saving solution they are a driving force behind efficiency in large-scale manufacturing. Whether in automotive, aerospace, or heavy machinery, aluminium castings are helping manufacturers achieve more with less, paving the way for faster, cheaper, and more sustainable production methods. Ready to upgrade your manufacturing process? Contact us today!