What is 5-Axis CNC Machining? A Comprehensive Guide
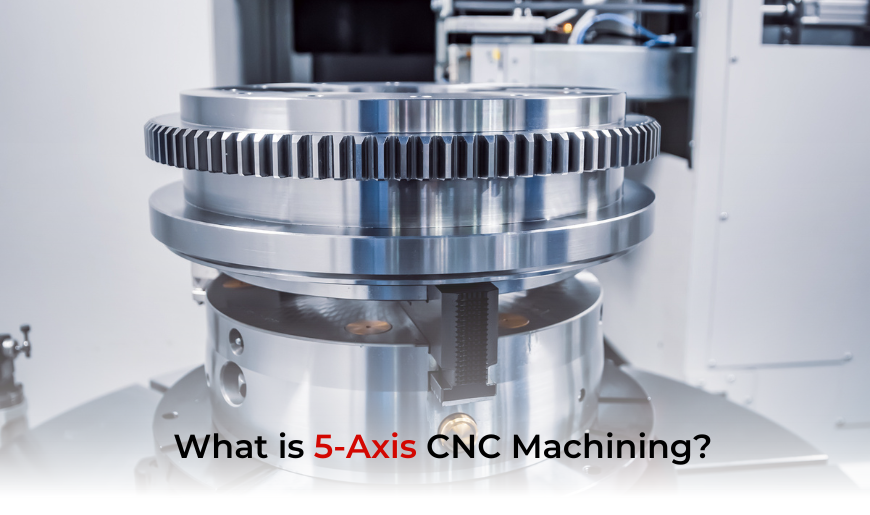
In manufacturing, where every fraction of a millimeter counts, the ability to craft complex, precise parts is what sets leading companies apart from the rest. Imagine creating a part that requires machining from multiple angles, without needing to reposition it over and over. This is where 5-axis CNC machining takes center stage a breakthrough technology that allows manufacturers to craft parts with exceptional accuracy and speed. So, what’s all the hype about 5-axis CNC, and how does it differ from traditional machining? Let’s dive into the world of this remarkable process.
Unlocking the Power of 5-Axis CNC
CNC machines, which are guided by computer programs, have long been essential in precision machining. The typical 3-axis CNC machine can move the cutting tool along three directions—left/right, up/down, and forward/backward. But for more intricate, complex shapes, these three axes just don’t cut it. 5-axis CNC machining takes things to the next level by adding two rotational axes, allowing the cutting tool to move in virtually any direction.
This additional flexibility means the machine can approach the workpiece from multiple angles without having to reset it. The result? Fewer setups, faster production, and the ability to create parts that would be near impossible with a 3-axis machine.
A Game Changer for Complex Designs
When it comes to intricate designs, 5-axis CNC machining is a true game changer. Take parts that require undercuts or complex curves things like turbine blades, engine components, or even surgical instruments. Traditional 3-axis machines struggle with such complexity because they can only access the part from a few limited angles. With 5-axis machining, the workpiece can rotate and tilt, allowing the cutting tool to access every corner and curve in a single setup.
This capability means that manufacturers can produce much more complex parts while maintaining high accuracy, all in a streamlined process. The ability to work on multiple sides of a component at once reduces the chances of errors and ensures that every part is crafted with exacting precision.
Efficiency at Its Best: Less Setup, More Precision
In traditional 3-axis CNC machining, parts often need to be removed, repositioned, and realigned to access different angles. This can lead to mistakes, wasted time, and inconsistent results.
With a 5-axis machine, the part remains fixed in place throughout the machining process, eliminating the need for multiple setups. This not only saves time but also boosts precision since the risk of misalignment is drastically reduced. Manufacturers can achieve high-quality results faster, making this method ideal for industries that demand both speed and accuracy.
Versatility for Tough Materials
5-axis CNC machines are designed to handle a wide variety of materials from soft plastics to hard metals like titanium and aerospace alloys. This versatility makes them a go to choice for industries that require complex parts made from difficult materials.
Whether it’s crafting engine components that need to be both lightweight and strong or producing surgical implants from biocompatible materials, 5-axis machining can tackle it all. The precision with which these machines work also means that they can minimize waste and increase material efficiency, especially when dealing with expensive or hard-to-machine materials.
Revolutionizing Critical Industries
5-axis CNC machining is particularly beneficial in industries where precision isn’t just preferred it’s essential. Aerospace manufacturers, for example, rely on this technology to create parts like turbine blades, which require extremely tight tolerances and intricate geometries.
Medical device manufacturing also reaps the rewards of 5-axis machining. Surgical tools, implants, and prosthetics often need to be produced with a level of detail and accuracy that 3-axis machines simply can’t offer. The ability to work with delicate materials like titanium while maintaining precision makes 5-axis technology indispensable in this field.
The Learning Curve: Mastering the Machine
As with any advanced technology, 5-axis CNC machining comes with its challenges. These machines are more expensive and technically demanding than their 3-axis counterparts, and operators need a deeper understanding of both the machinery and the materials being worked with.
However, for companies willing to invest the time and resources into mastering 5-axis machining, the payoff is enormous. The speed, accuracy, and flexibility this technology offers far outweigh the initial learning curve and setup costs.
The Future of Precision Machining
In the ever-evolving world of manufacturing, 5-axis CNC machining stands at the forefront of technological innovation. As industries continue to demand higher levels of complexity and precision, the importance of these machines will only grow. From aerospace to medical devices, automotive to defense, the ability to craft parts with extreme accuracy from a variety of materials is a competitive edge that no manufacturer can afford to overlook.
In short, 5-axis CNC machining is changing the way we make things. It’s not just about precision it’s about pushing the limits of what’s possible in manufacturing, creating parts that were once thought to be beyond reach. And as technology continues to evolve, it’s clear that 5-axis machining will play an even bigger role in shaping the products of tomorrow.